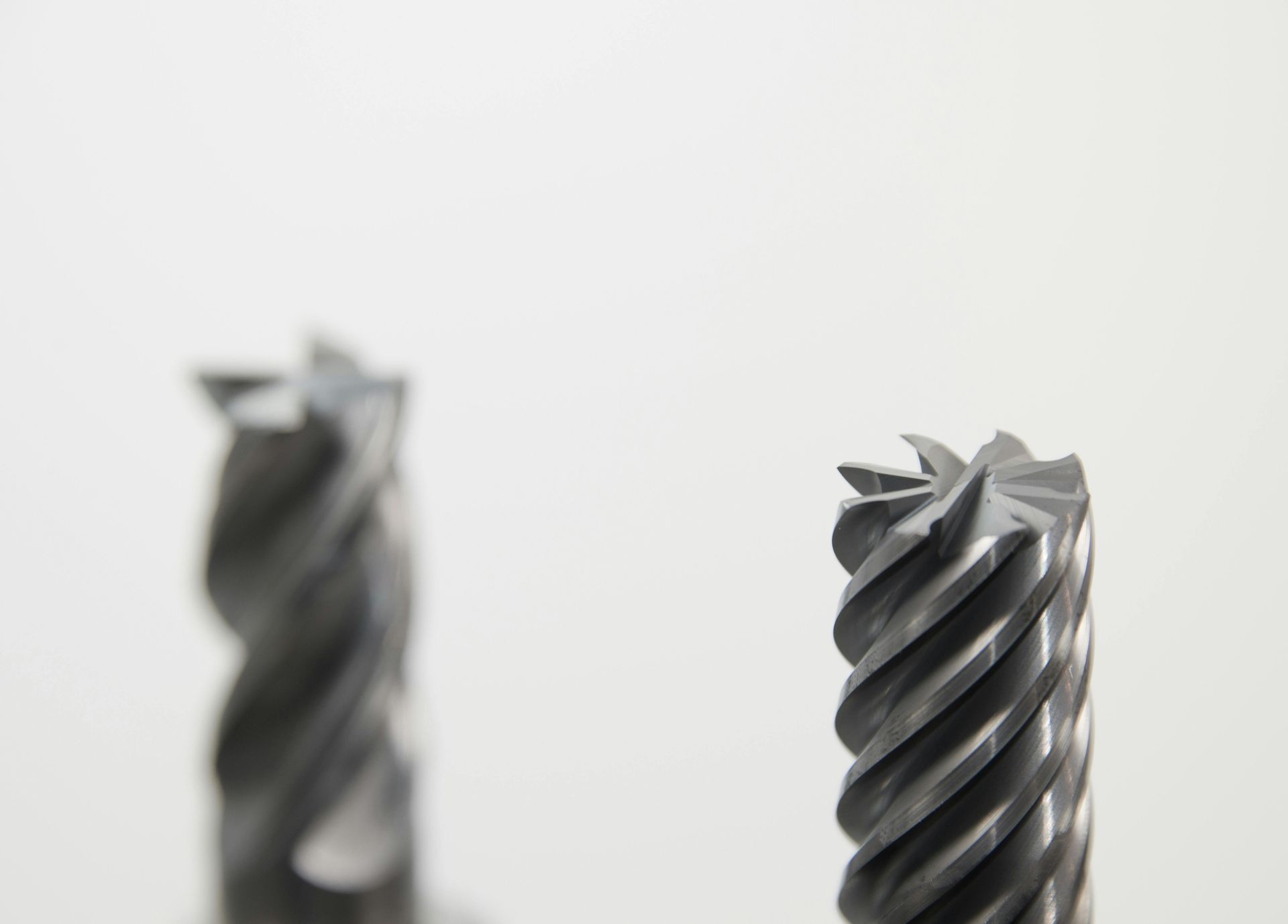
5 Operational Challenges for Small Manufacturers and How to Overcome Them
Small manufacturers are the backbone of American industry, but running lean comes with its own set of operational headaches. From labor shortages to inefficient systems, these problems don’t just cause stress, they chip away at margins, timelines, and customer satisfaction.
At ATLATL Business Solutions, we work closely with blue-collar business owners and manufacturing leaders to implement smart systems that scale. Below are five of the most common operational challenges we see and how to overcome them before they impact your bottom line.
1. Inconsistent Production Schedules
Small manufacturers often juggle custom jobs, seasonal swings, and shifting customer deadlines… all of which create chaos in the production process.
How to Fix It:
Implement a production scheduling system that integrates with your inventory and sales data. This helps align your shop floor with actual capacity and delivery expectations. A Fractional COO can help you choose the right platform and build workflows that stick.
2. Poor Inventory Management
Overstock ties up cash. Understock causes delays. Either way, poor inventory control creates costly inefficiencies.
How to Fix It:
Adopt a real-time inventory management system that integrates with procurement and production. Set reorder points, conduct cycle counts, and simplify your supply chain with strong vendor relationships.
3. Lack of Standard Operating Procedures (SOPs)
If your processes only exist in someone’s head, your business isn’t scalable. Quality drops, training slows down, and you lose critical knowledge when key team members leave.
How to Fix It:
Start documenting your core processes beginning with job setup, safety checks, and quality control. Visual SOPs and work instructions posted on the floor can drastically improve consistency and productivity.
4. Labor Shortages and Skill Gaps
Finding and keeping skilled workers is harder than ever. Without enough trained hands on deck, productivity and morale suffer.
How to Fix It:
Develop an in-house training program. Partner with local trade schools. Cross-train your workforce to build flexibility. And tighten your hiring process with job descriptions that clearly reflect your values and expectations.
5. Lack of Operational Visibility
If you’re still running your shop on spreadsheets and paper logs, you’re flying blind. Without real-time data, it’s impossible to make fast, informed decisions.
How to Fix It:
Track KPIs that actually move the needle like scrap rate, on-time delivery, and OEE (Overall Equipment Effectiveness). Use dashboards to visualize trends and hold teams accountable. Visibility leads to action and anything worth doing should be measured. What gets measured gets done.
Wrapping Up: Don’t Let Operations Hold You Back
These challenges are common but they don’t have to be permanent. At ATLATL Business Solutions, we help small manufacturers streamline processes, reduce waste, and scale sustainably through fractional COO support and hands-on operational consulting.
Let’s build a shop that runs smoother and scales smarter.
👉 Schedule your free consult now
👉 Learn more about our Fractional COO Services